A new software integration tool attacks what I call “workplace technology interplay denial.”
Above: At BPG Designs, plenty of screens are filled with integration software.
Through our smartphones, we are now integrated with all the people we know (and don’t know); we have integrated our work spaces with our home lives; and we can even track our geographic position and plot the quickest route to work. The importance and influence of this integration can be seen throughout our lives.
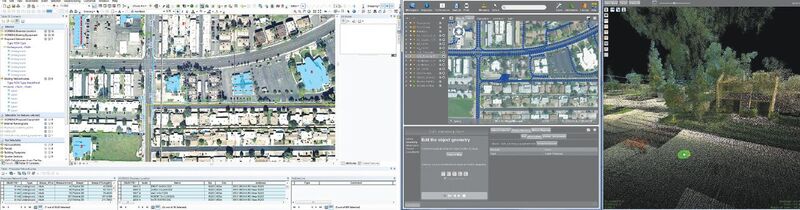
This double screen shows ArcGIS network design and Orbit Mobile Mapping Feature Extraction solutions working side by side.
The question now is: Why are we not as successfully integrated at work when it comes to the technology solutions we leverage every day to satisfy our clients’ needs? If my mother can send me a Snapchat but I’m unable to get two different mapping software packages to talk, we have a problem.
If you have a complex program directory–or If you’ve ever worked on a CAD project that needed to be integrated into a GIS quickly and properly–you know my pain! It baffles me that we live in this world of “workplace technology interplay denial.”
This used to be the scenario at my workplace, BPG Designs (BPG), located in Tempe, Arizona. To give you some background, BPG is a medium-sized design and construction company focusing mostly on the telecommunication and utility markets. The industries BPG works in are all fast-paced and reactive and need high-end attention to detail.
The group I manage at BPG is one of the four main departments of the mapping, design, construction, and networking technologies’ teams. In the mapping group we focus on survey, mobile mapping, static lidar collection, BIM, UAV dataset processing, and custom GIS-mapping solutions. The programs we use daily include AutoCAD, ArcGIS Server, Geoclean, Mobile Mapping Office, Spatial Factory, Virtual Geomatics, Orbit GT, Carlson CAD, Pix4D, Revit, and Cyclone.
As you can see, we use a plethora of software and hardware solutions in our daily workflow. We are not tied to a single brand or process; rather we use the right tool for the job.
However, having this many software packages has proven to be extremely difficult to manage. The integration of these systems, files, and services with a team of 20 mapping specialists and nearly 50 drafters has been a bit of a headache, to say the least. We needed a better way to help manage this.
Software Integration
We found a solution in Orbit GT, which plays nice with the others. Orbit Feature Extraction immediately became our go-to solution for lidar feature extraction, replacing other unstable programs. Orbit’s software accepted lidar data from two different mobile lidar systems and two processing software packages with no hassle. We can export data from Orbit in different formats that can be accepted by most other software that our company uses.
The extracted data also went right into our previous list routines in Carlson CAD, meaning there was no change in workflow for QC and submittal processes.
Orbit also provided mobile mapping plugins for ArcGIS and AutoCAD that fit into our workflow, and the Mobile Mapping Publisher software helped us present our lidar data to end users, both inside and outside our company. With point features created along our mobile mapping trajectories, we could easily calculate X and Y locations that plug into a hyperlink that would lead the user right to the exact location in the lidar data that they were looking for.
This solution tied right into our ArcGIS web apps that we present to clients already, so the only change they saw in the deliverables was a better lidar viewer.
Workflow Improvement
But the real magic started when we began to integrate Orbit, SQL Server, and ArcGIS. By creating a database connection in ArcMap to the SQL Server database that Orbit Feature Production already populates, we became power users. All feature-extraction jobs can now be cast real time in ArcMap or ArcGIS Online. Feature extractions can be tracked from a performance standpoint, with up-to-the-minute statistics of features extracted per minute or a calculated average of distances extracted over time.
These XY features can also be made into ArcGIS Online Feature Layers, allowing extractions to be presented to non-ArcMap users through web maps and web apps.
Surveying for Cable
Here’s a project where Orbit GT really helped. BPG Designs was tasked to complete the survey and design work for the installation of a 40-mile span of fiber optic cable along Highway 79, a rural route that runs in Arizona from Cooledge to Oracle Junction. It’s used by truck drivers to avoid busy Interstate 10 as well as by off-road enthusiasts for the many trail heads along the route.
Highway 79 crosses high desert and presents many challenges for the construction of underground utilities. The desert is scarred with washes, and there is no constant grade that could be followed with boring machines. The dense brush makes the use of trenching machines very difficult, if not impossible. In order to complete construction, a detailed survey of the planned route was needed for designing a boring plan that’s feasible and efficient.
BPG Designs took on the task by using multiple surveying techniques and technologies. We used Topcon GNSS network receivers to locate monumentation along the route, including section corners and brass caps. We used a Topcon IP-S2 mobile lidar system to collect data along the roadway, including all road features and assets along the side of the road.
We also used a senseFly eBee UAV to capture a high-detail topographic survey of the project area. The data from the UAV was used to capture the location and depth of all major washes that could pose a problem in construction.
We processed and combined all of the data to create a seamless, real-world representation of the environment on a desktop computer. We used Orbit to locate and extract physical features in the right of way. We collected the edge of pavement, monumentation, utility poles, fence lines, and other features and exported them for use in AutoCAD, where the data were combined with the monumentation collected with the GNSS receivers to improve spatial accuracy.
The data from the eBee UAV was processed into a high-resolution orthophoto and a point cloud in Pix4D. After classifying the point cloud to obtain a ground surface, we used ArcGIS to create a digital elevation model and contour lines. The surface and contour lines were then combined with the data in AutoCAD. The resulting collection of data from disparate sources allowed the engineers at BPG Designs to create permitting drawings. Orbit did not drive or change our workflow; instead, it nestled itself right into all aspects of it, integrating parts of our work so that we couldn’t have done without it.